Perhaps the only thing more annoying for a generator owner than having a generator not start at all is having it repeatedly stall shortly after starting.
When the power is out and you need to light things up in your house to calm your family down, the worst thing is a generator that keeps giving you false hope that it’s going to run and promptly stalls, dashing your dreams away from you.
As a general rule, a generator will stall for any of the following seven reasons: bad fuel, clogged jets in the carburetor, a dirty air filter, faulty spark plug, a compromised bond between the float needle and seat in the carburetor, a faulty low oil indicator shut off, or a stuck choke butterfly valve.
Reason for Generator Stalling | How to Fix |
---|---|
Bad Fuel | Drain fuel and replace with fresh fuel that has been treated with a fuel stabilizer like SeaFoam |
Carburetor Jets Clogged | Remove air filter assembly; turn off fuel valve; drain carburetor bowl; remove carburetor; remove bowl; remove main jet and emulsion tube (clean with carb spray and a small wire); remove pilot jet and clean with carb spray and a small wire |
Dirty Air Filter | Remove air filter and test engine — if it runs better then replace the air filter |
Bad Spark Plug | Remove spark plug boot, remove spark plug with deep-well socket, reconnect spark plug boot, ground spark plug threads on the engine block, pull recoil and inspect the strength of spark — clean with wire brush or replace if necessary |
Compromised Bond Between Float Needle and Seat in Carburetor | Remove air filter assembly; turn off fuel valve; drain carburetor bowl; disconnect carburetor; remove carburetor bowl; remove float pin and inspect the needle and seat for a deformity in the rubber (replace if necessary), varnish from bad gas, or debris |
Faulty Low Oil Indicator Shut Off | Visually verify that generator has the proper amount of oil, disconnect wire at first disconnect point above the oil indicator probe |
Stuck Choke Butterfly Valve | Remove air filter assembly to access, spray top and bottom ends of butterfly valve with carburetor cleaner, gently work it back and forth, ensure choke lever is properly connected |
Let’s jump right in
1. Bad Fuel
Fuel problems are definitely at number one when it comes to things to check if your generator is not starting or stalling. If you’ve had untreated gasoline in your gas tank for over a month the performance is going to start to decline and after about 3 months you might not get your generator running or it might stall like crazy.
If you’re not sure when the last time fuel was added to your generator or you’re not sure how long that fuel has been stored in that red plastic gas can, then it is best to get fresh fuel. I have an entire article here about how to drain bad gas out of your generator and what to do with it.
When gas goes bad it’s essentially attacked by oxygen in the air and it evaporates off the volatile “light ends” of the gasoline which are the best thing for the engine and lead to the best combustion.
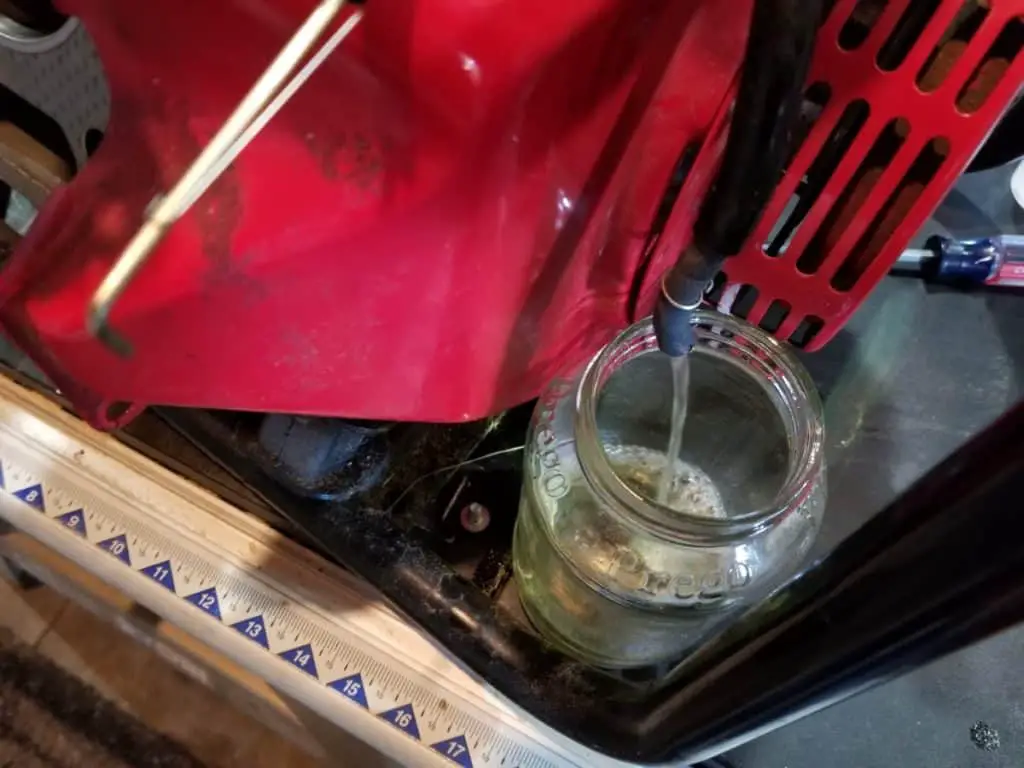
The oxygen will react with the hundreds, if not thousands, of additives that are in your gasoline and will start to change the chemical properties of them and make your gasoline gum up and turn into a varnish.
If you use an ethanol blend gas especially, you have a high risk of having water mix in with your gasoline as the ethanol will bond with moisture in the air over time.
All of these things lead to your engine not combusting properly and when it can’t generate enough consistent power then it will stall out.
It’s best to swap out your gasoline with an ethanol-free blend. I have a link to a website here that will show you where to get ethanol-free gasoline anywhere in the United States and Canada.
Also, make sure that you use a fuel stabilizer such as Stabil or SeaFoam (my personal favorite, link to Amazon) immediately after purchase. Once you do this your gasoline will last easily for 1 to 2 years without problem.
2. Carburetor Clogged Up
So many things can go wrong with your generator’s carburetor that it’s not even funny. If you’re new to small engines the carburetor can seem like an insurmountable obstacle, but I assure you it is not that complicated.
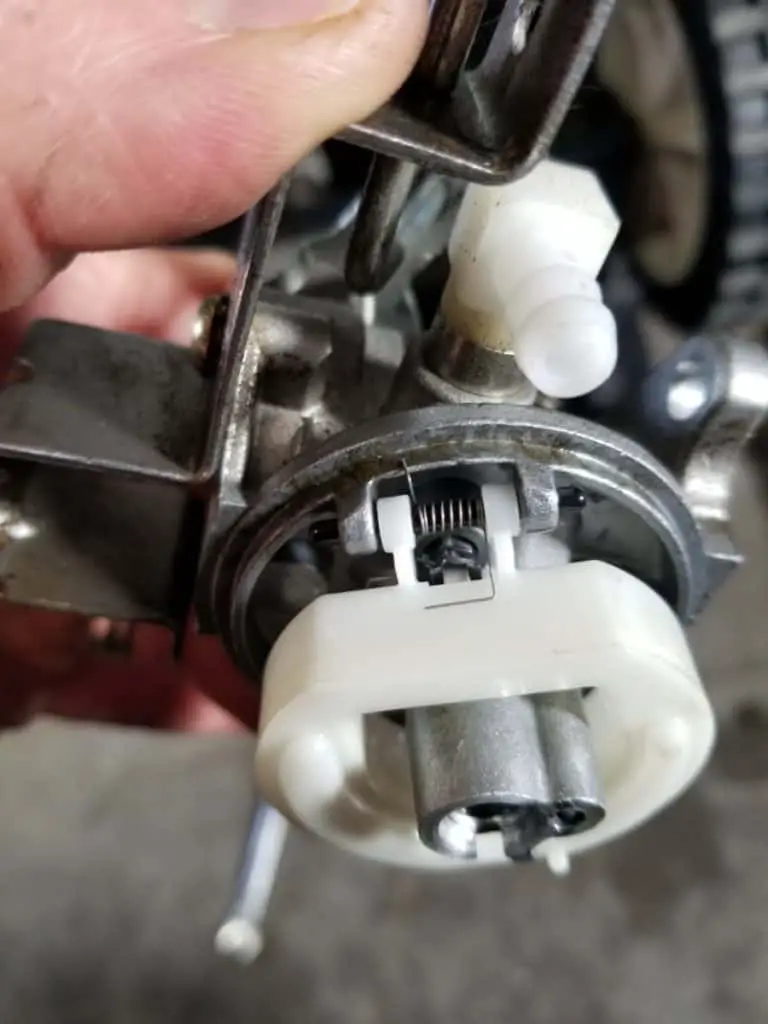
You just need to first understand that your piston, as it cycles up-and-down in the cylinder, acts as a pump. When the piston goes down it sucks in air and fuel through the carburetor to fill a volume about the size of a spaghetti jar. When it pushes back up it expels that out the exhaust and it does all of this at 3,600 RPM which is faster than your eyes or mind can even comprehend.
The carburetor is full of tiny ports and jets that can easily become clogged or restricted with any piece of dirt or stale gasoline that has turned to varnish or sludge. Even just a small restriction of a jet or a port and not a complete blockage can cause your generator to stall.
The first time I serviced a carburetor it took me probably over an hour and that’s mostly because I didn’t even understand how it functioned in the first place. Now I can service one in about 15 minutes or less and it’s no big deal. I have an entire article here with photos and a step-by-step video that guides you through how to remove, clean, reassemble, and reattach your carburetor to your generator.
3. Clogged Air Filter
Checking your air filter is one of the fastest things you can do as it’s usually just a cover that is held on by either 2 screws or 2 clasps.
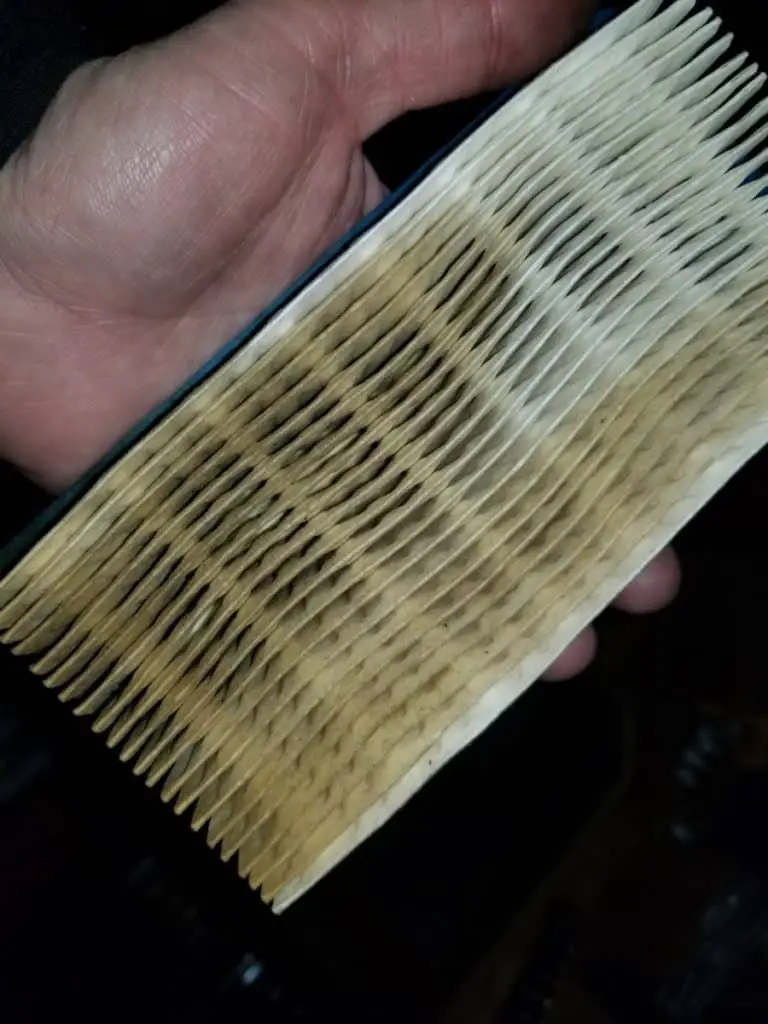
Simply remove them and check the state of health of your air filter. If it is absolutely choked full of black dirt then you need to get rid of it and replace it with a new one.
A clogged air filter restricts the amount of air that gets into your combustion chamber in the engine and leads to a very rich mixture which means that has more gas than air. This causes an engine to run inefficiently and lose power which can make it easily stall out.
4. Bad Spark Plug
Another easy thing to check is your spark plug with a spark plug remover tool or a deep-well socket (with the diameter being specific to your particular spark plug).
Once you remove it, check to see if it has too much carbon built up and that the gap between the two nodes is correct. You can even check for a spark by holding onto the rubber boot and placing the metal threads of the spark plug against the valve cover (which is made out of metal) to ground it.
Gently pull on the recoil start and see if you have a spark.
Quick warning, if you hold on to the threads of the spark plug when you pull the recoil chord you will shock yourself.
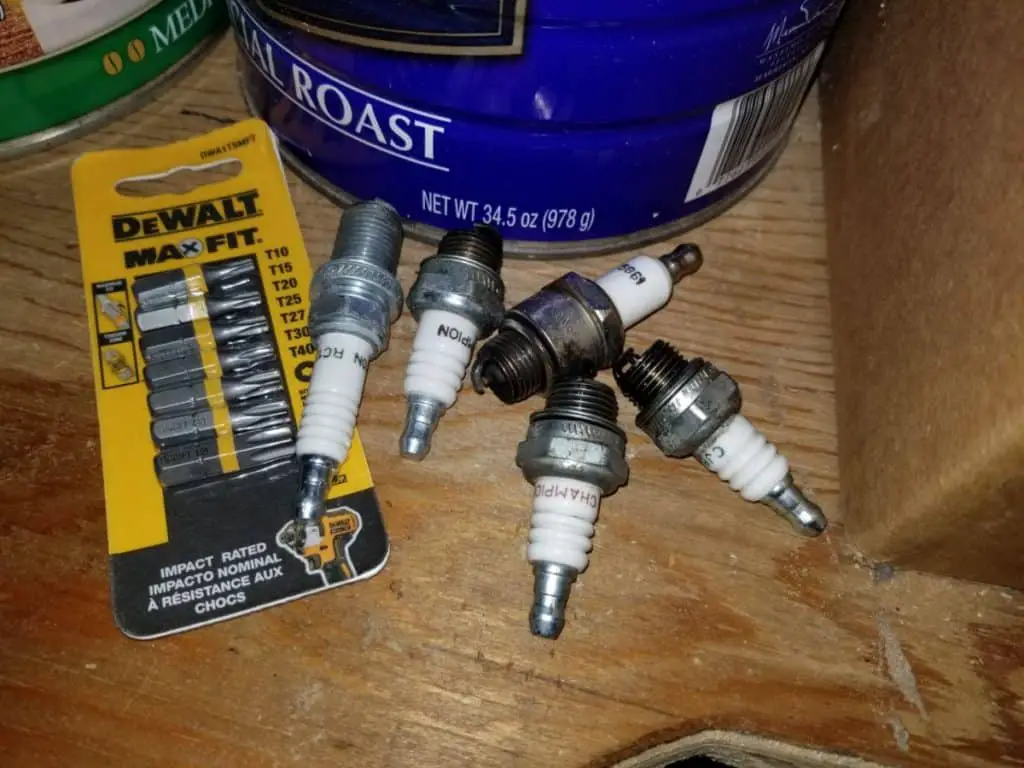
A spark plug that is covered with carbon or is giving off a weak spark can easily lead to stalling in the engine as incomplete combustion will happen inside the combustion chamber.
5. Flooding from a Bad Float Needle Valve
I actually have this happen to me in two small engines that I’ve repaired recently and that is a case of flooding occurring in the combustion chamber due to a float needle valve that is not seating properly.
In your carburetor there is a float that regulates the amount of gasoline that can enter into the carburetor itself and then when the float raises up it pushes a rubber-tipped needle into a metal seat (or a metal needle into a rubber seat) to create a proper seal and stop the flow of incoming gasoline.
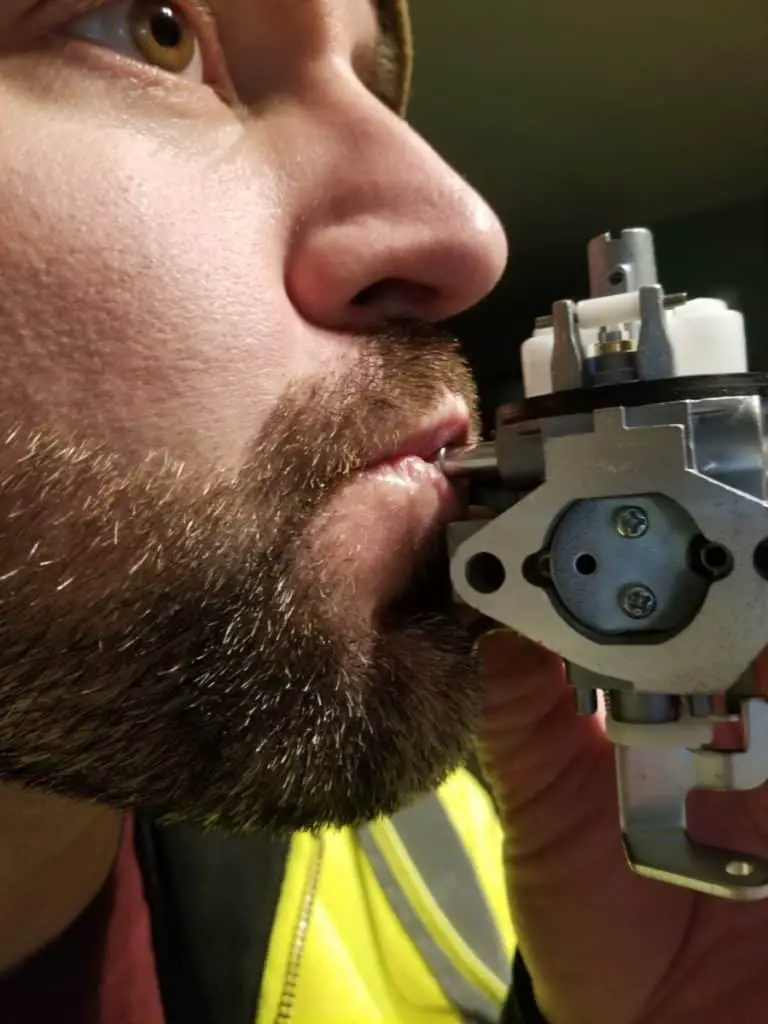
If there’s a piece of dirt or if the rubber on the needle became a little deformed then gasoline will continue to trickle by and overflow the carburetor. As the gas rises up it will run out either the air filter side or back towards be combustion chamber depending on the angle that your generator is at.
In my case I was able to start a generator and a snow blower for a short amount of time (maybe under a minute) and it was running very rich and then stall out and then it would be unable to be started again for quite a while.
As soon as I fixed the float needle everything ran perfectly. Again I have a video and article here to guide you through step-by-step how to take apart your carburetor and clean out the float needle valve.
6. Faulty Low Oil Indicator Shut-Off
Usually this problem will just lead to an engine not starting at all, but it can create stalling in certain cases.
If you look near the bottom of your crankcase where you feed the oil you’ll see some wires coming out and those lead to the low oil indicator shut-off float that’s inside your crankcase.
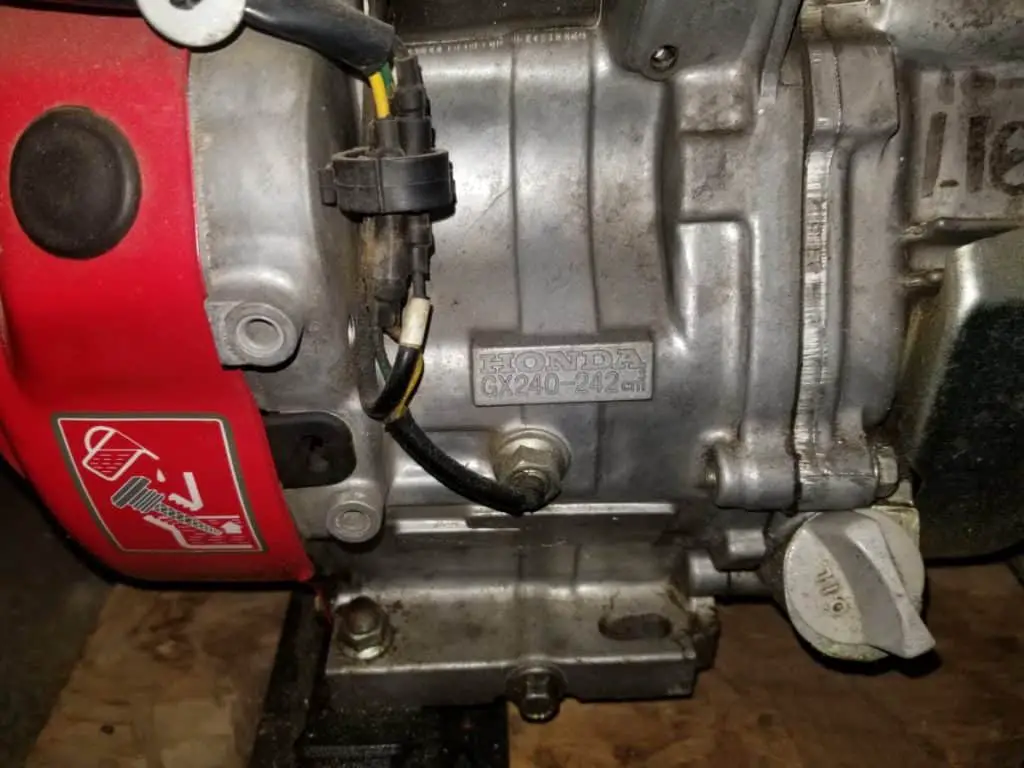
Generally, this float gets stuck in one position or another and relays a message to the generator to not start because there’s not enough oil in it (even if there is).
The problem is that sometimes when you free it and get it working again it’ll still get hung up somewhere as the engine is warming up and the oil is changing temperatures.
So, if all else fails and you can’t find what’s wrong, try following the wire up to a disconnect point and unplug it to see if your engine runs fine. It’s not a usual problem but it’s worth a shot if none of the other steps have been working.
7. Stuck Choke
You can also check to make sure that your choke valve on your carburetor is not stuck in the closed or half-choke position.
This can happen if your lever that connects to the butterfly valve gets disconnected or if there’s too much of a varnish from bad gasoline that has caused the choke valve to stick.
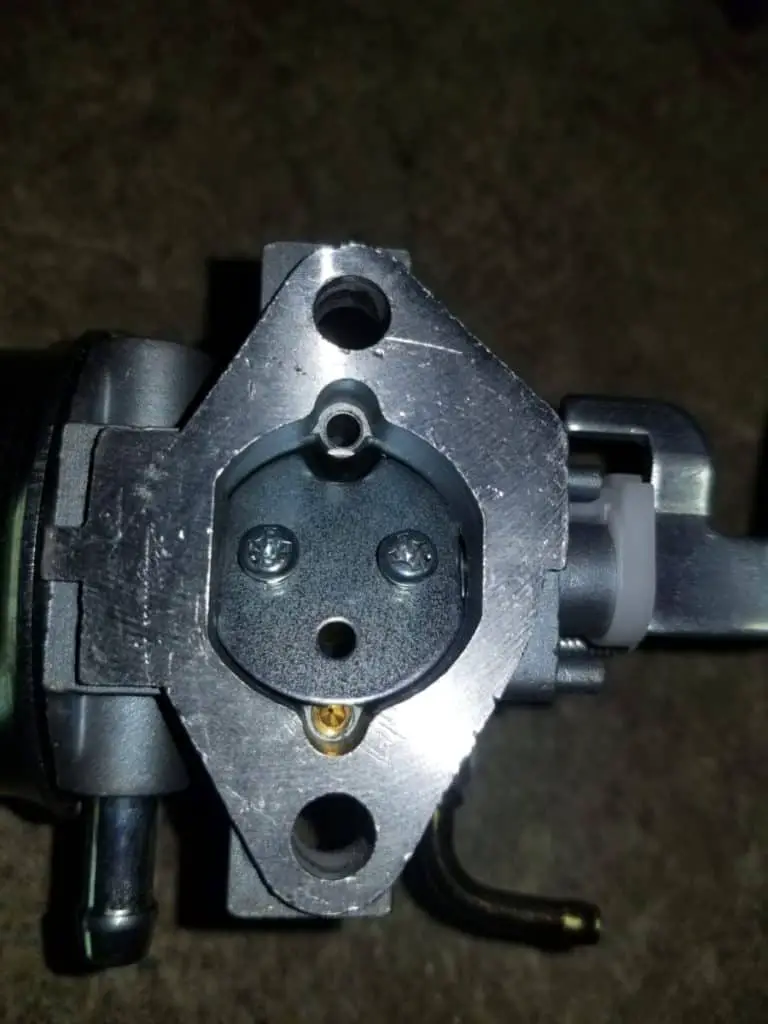
If your engine is warming up and calling for more air and your choke is in the closed or half-choke position and won’t open up, then your engine will run rich and be very likely to stall.
If you find that your choke is not moving just reconnect the lever to it (if it’s detached) and if it’s physically stuck then go ahead and spray some carburetor cleaner liberally around it let it soak. Work at it with a cotton swab along the varnished areas as you gently wiggle the choke lever/valve to free it up.